Fix the root cause of No-Call No-Show with help from TeamSense
Table of Contents
- What is Absenteeism?
- Why is attendance important in manufacturing productivity?
- How much does lost productivity caused by absenteeism cost the US each year?
- 5 Ways Absenteeism Impacts Manufacturing Productivity
- How to reduce absenteeism in the manufacturing industry
- TeamSense Makes Communicating Absences Simple
You probably already know that absenteeism and productivity don’t go hand in hand in any industry. But while employee absenteeism might just be an annoying HR issue in any other industry, in manufacturing, absenteeism means decreased productivity, increased costs, and potential safety hazards. Plus, a lack of manufacturing productivity can really tank your bottom line.
The impact of absenteeism on manufacturing productivity has far-reaching effects. We'll cover what these are and how to avoid them, but first, let's define absenteeism.
What is Absenteeism?
Absenteeism in the workplace happens when an employee makes a habit of not showing up to work. This is also known as an unplanned absence and is different from a planned absence (like a team member taking some much-needed approved PTO). In a manufacturing facility, unplanned absences will pop up from time to time, but excessive unplanned absences are considered absenteeism.
Absenteeism is a major issue in the manufacturing industry. And on any given day, almost 1 in 10 employees are absent on days they are scheduled to come into work.1 And that’s when the bottlenecks start happening.
Absenteeism can lead to reduced output, increased costs, decreased morale, safety concerns, and decreased quality of work. All of these factors can result in missed deadlines, delayed shipments, and, ultimately, a decrease in the overall operational efficiency of your manufacturing operations.
Why is attendance important in manufacturing productivity?
When it comes to increasing your manufacturing process, productivity, efficiency, and output—attendance is vital. If you want to maximize efficiency, increase output, and make sure you hit your production targets and that there are no delays on the line, you need to have every role filled. When employees are absent, it throws a wrench in the whole operation. It can lead to delays and bottlenecks in the production process, which can hurt the company's reputation and profits.
And let’s not forget about safety reasons and employee morale. The manufacturing industry can be a dangerous place to work. When employees are absent, it can put an extra strain on those who did show up for work—increasing the risk of accidents and injuries, not to mention the feelings of resentment and frustration among team members. Companies can create a positive and productive work environment that benefits everyone by making sure everyone shows up to work on time, ready to go.
Interested in other issues facing the manufacturing industry? Download our free resource, 2023 Trends and Forecasts for U.S. Manufacturing, to learn more.
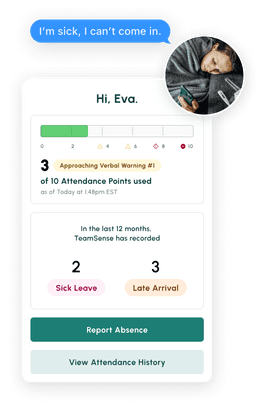
Is your call-in process terrible? Text reduces no-shows and absenteeism by up to 40%.
Don't believe us? Check out this case study to see how this 3PL benefited.
How much does lost productivity caused by absenteeism cost the US each year?
The costs of absenteeism can really add up. A recent study estimated that absenteeism costs U.S. employers $225.8 Billion each year.2 That number takes into account the direct costs of paying absent employees, as well as the indirect costs that come along with reduced output and decreased efficiency overall.
And from an employee standpoint alone, absenteeism costs U.S. employers $3,600 per hourly employee per year.3 As if that wasn’t enough of a gut punch already, the estimated loss of workforce productivity due to unplanned absence clocks in at nearly 37%.4 Those are some crazy numbers!
5 Ways Absenteeism Impacts Manufacturing Productivity
For managers in the manufacturing industry, absenteeism is one of the biggest challenges they have to face. While you might think that an employee missing work a lot is a personal issue for that team member, it actually impacts the entire production output of your facility. When employees miss work, it has a ripple effect and can have a significant impact on improving manufacturing productivity and, ultimately, your bottom line. Here are five ways absenteeism impacts manufacturing and productivity in manufacturing.
1. Reduced Output
When employees are absent, fewer people are there to do the work. This can lead to reduced output, increasing efficiency and lower productivity levels across the board. It can also mean missed deadlines and delayed shipments, putting you behind your target goals and causing stress in trying to make up for the loss.
2. Increased Costs
Absenteeism can lead to increased costs for the company. This might include paying overtime to other employees to cover the work or it costs money hiring temporary employees to fill in the gaps. Both of these options can be expensive and will eat into your profits fast.
3. Decreased Morale
When employees are absent, it can put a strain on the remaining team members who have to pick up the slack. In fact, one study found that, on average, co-workers were 29.5% less productive when providing coverage for a “typical absence day;” supervisors were 15.7% less productive.5
Not only does team productivity suffer, but the extra workload they take on can lead to stress and burnout. After covering for continually absent employees, employee productivity of your remaining team members will likely take a hit in morale and job satisfaction. This is something you’ll need to pay close attention to since employee engagement and burnout impact absenteeism and employee retention rates. In the middle of declining productivity, the last thing you want on your hands is a staff shortage due to employee turnover.
4. Safety Concerns
Safety is a top priority in the manufacturing industry, with leaders always looking to keep factory floors safe, maintain OSHA standards, and keep daily manufacturing floor operations compliant at every level. When employees are absent, it can lead to safety concerns as there may not be enough people to properly operate machinery or complete tasks safely. Believe it or not, OSHA’s top 10 most frequently cited safety violations are actually preventable with the right foresight and precautions, so take the steps you need to make your team feel safe on the floor.6
5. Decreased Quality
When employees are absent, expect a decrease in your team's work quality. This usually comes from rushed tasks or errors made by team members covering for their absent colleagues and trying to keep up with demand. Honestly, those hard-working team members picking up the slack are rock stars. They’re doing their best with the cards dealt to them that day. It's not their fault that the output quality is suffering; they just need more manpower on the floor.

How to reduce absenteeism in the manufacturing industry
So, what can you do to give your manufacturing productivity a boost, reduce costs, and cut back on absenteeism? Well, a lot, actually! Here are eight ideas on how to increase productivity and reduce absenteeism in your manufacturing plant:
Have a clear attendance policy.
Have you given your attendance policy a refresh lately? Make sure it spells out your employee attendance expectations and discipline policy loud and clear. If you want to cut back on absenteeism and improve productivity at your company, your employees need to understand the consequences of absenteeism and the importance of showing up to work on time.
Incentivize attendance.
Have you ever thought of offering incentives for your team to show up to work? You can do this by letting employees accrue extra PTO and sick time throughout the year or give PTO as an award to the person with the least unplanned absences on your team. Get creative and make a competition out of it too! At the end of the day, you’ll encourage attendance and boost team morale while you’re at it!
Increase employee engagement.
Did you know an engaged employee is less likely to be an absent employee? It’s true. A high level of employee engagement can reduce absenteeism by as much as 81%.7 With numbers like that, the manufacturing industry should begin spending more time and energy focusing on improving employee engagement numbers any chance they get.
So go ahead and schedule some employee bonding time to boost team morale and spruce up the break room. Just a few positive tweaks can mean the difference between an engaged employee and one who is checked out.
Implement a wellness program.
Sometimes absenteeism stems from an employee slacking off, and sometimes it’s related to a sickness that can’t be helped. While it’s true you can’t stop the common cold from hitting your team, you can help keep it at bay. By promoting healthy habits and lifestyles, you can help reduce the number of sick days your employees take.
This will look different at every company. Maybe it means incentivizing getting an annual flu shot or setting up lunch break walking groups. These small efforts might not keep your entire plant immune from sickness all year, but they can go a long way to cut back on the time they’re out. And remember, with more employees present at work, the business can continue as usual with little output disruption and reduce downtime.
Pay attention to employee burnout.
Employee burnout can impact all employees across the board, but it’s especially high in manufacturing companies. A study published by Social Psychiatry and Psychiatric Epidemiology found that mental health issues are 36 percent more frequent in manufacturing employees than the national average.8 Let this number be a wake-up call to encourage you to have a greater focus on team member well-being and take a holistic approach to care for your hourly employees.
Encourage your managers to look for warning signs of employee burnout and pay attention to heavy workloads. In this situation, knowledge is truly power. Identify and address the sources of stress in your workplace which can contribute to employee absenteeism, anxiety, and burnout. Then seek out ways to actively lessen those stressors however you can.
Offer flexible scheduling.
Life happens, and things come up. Employees who feel like they have flexibility in their schedule might be less likely to need to take time off work or develop a habit of being absent. Talk to your employees about their shift schedule and let them pick a schedule that works best for their life. Consider allowing your employees to work flexible hours and make up time when they need to. This can help them balance work with personal responsibilities and may even cut back on the amount of no call no shows you have.
Improve workplace safety.
This is one that often gets forgotten, but workplace safety plays a direct role in absenteeism. Following safety precautions to the letter can drastically cut back on absenteeism and boost manufacturing efficiency and improve manufacturing productivity too. By creating a safer work environment, you can see greater productivity and reduce the risk of workplace injuries and illnesses, which can lead to absenteeism. Not only that, but your team will be more likely to come to work when they feel safe performing their duties.
Invest in absence management software.
If you want real insights about absenteeism at your manufacturing facility, you need absence management software that has automated systems you can rely on to tell you who’s in and who’s out for the day. Plus, the insights you get from data tracking and monitoring attendance trends are incredibly valuable. If you want to run an efficient production line, you need easy-to-use absence management software that doesn’t take a tech wizard to operate it.
TeamSense Makes Communicating Absences Simple
The truth is, your team shouldn’t have to jump through hoops just to let you know they’ll be absent. In fact, if your call out process is too complicated, you could have plenty of no call no shows just because your call off protocol is daunting. TeamSense lets your team notify you of their absence using straightforward text messaging—no fancy apps that nobody knows how to use here. TeamSense’s text-based employee call off system lets your team communicate easily with you, so you can keep your manufacturing line operations running smoothly and efficiently.
Save Hundreds of Hours A Year With TeamSense

See how TeamSense saved HelloFresh 3-4 hours per day managing attendance through text. Read the case study and book your demo today!
About the Author

Sheila Stafford, CEO of TeamSense & AI in HR Innovator
As CEO of TeamSense, Sheila Stafford is at the forefront of transforming HR for frontline teams through AI-driven solutions. With a commitment to enhancing employee relations and simplifying workforce management, Sheila leads TeamSense in pioneering advancements that empower both frontline employees and HR teams. Her visionary approach combines cutting-edge technology with a thoughtful focus on enhancing human connection; Sheila strategically implements AI where it adds the most value while recognizing the critical role of personal interaction and ensuring that human engagement remains central when it matters most. Under her leadership, TeamSense is redefining how companies support and engage their frontline teams for a more connected, efficient workplace.